
There are also quite a lot of PCB depaneling tools: Mousebites can also easily be a 2nd or 3rd choice. Mousebites that combine 20×20 PCB’s in a panel very likely have a different geometry then mousebites that hold just 3 PCB’s in a panel. I also find their single recommendation doubtful. I’m guessing sparkfun uses a lot of panels anyway and these tests could easily have been combined with PCB’s that end up in real products instead of the garbage bin. I find it quite wasteful to order all those PCB’s just to test mouse bites. The solution: any SMT decoupling caps that were close to the pcb edge were turned so that their long axis was parallel to the pcb edge, so the stresses of depanelising the pcbs did not damage them. The failing caps were causing our power reservior capacitor supply to discharge in a matter of minutes. Line powered devices rely on the 50uA that you can draw from the phoneline to keep them powered. Microscopic cracks were forming inside the capacitor, and in damp/humid condtions the capacitors were absorbing moisture and, worst case, becoming more like 1K resistors. We finally tracked it down to some 0.1uF 0603 decoupling capacitors, that were being damaged when the pcbs were broken out of the panel. Posted in how-to, Science Tagged breakaway, breakaway tab, empirical, mouse bites, pcb, perforation line, v-groove Post navigationĪbout 20 years ago, I worked for a company that made a high volume telephone dialler product.Īfter about the first 100,000 were produced, we found that we were getting some unusual failures.Īfter some analysis we found that these were units that had been located in cold and/or damp locations, such as a basement or an old house with solid walls. When it comes down to it, the best numbers will ultimately be the ones that your process or fab house can most efficiently handle, but ’s numbers should not steer anyone wrong, and it’s fantastic to see this kind of work go into refining such a common PCB feature. What about thickness of PCB? tested boards both 0.8 mm and 1.6 mm thick, and while different amounts of torque were needed to snap the boards apart, things still worked as expected regardless of PCB thickness. To fine tune, suggests increasing the spacing between holes to add strength, or just adding additional tabs. Holes should be placed slightly differently depending on whether one wishes to optimize the cosmetic appearance versus the physical smoothness of the board edge, but those numbers are the core of the guidelines.
BREAKAWAY CLT 2022 FULL
The full details are available in Building a Better Mousebite (PDF download) but the essence of the recommendations are: 0.015″ unplated holes, spaced 0.025″ apart (center-to-center), tabs a maximum of 0.118″ wide (so as to be compatible with depanelizing tools), and holes that extend into the corners of the breakaway tab to avoid sharp edges.

This is best for boards that are rail-mounted, or have tight enclosures.ĭata on designing mouse bites was sparse and a bit inconsistent, so decided to figure it out empirically and share the results.
BREAKAWAY CLT 2022 FREE
Placing holes tangent to the board edge (as shown above) isn’t the prettiest, but keeps PCB edges free from protrusions.
BREAKAWAY CLT 2022 HOW TO
We’ve covered panelizing PCBs in this way before, but this is the first time we’ve seen someone seriously look into how to create optimal breakaway tabs.
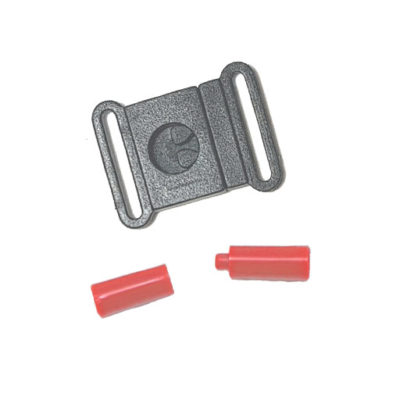
On top of that, edges must also break cleanly. Too weak, and the board may break or twist before its time. Too sturdy, and breaking apart is a hassle. However, it can be tricky to get results that are just right. The nice thing about creating a perforation line (or “mouse bites”) is that drill hits are a very normal thing in PCB production, which makes creating this kind of breakaway tab a very straightforward and flexible method. But what’s the best size and spacing of holes to use? Sparkfun’s spent some $400 on PCBs to get some solid answers by snapping each of them apart, and judging the results. V-grooves that go most of the way through a PCB are one way to go about this, but a line of perforations along which to snap a tab is another. Most of us are familiar with the concept of producing PCBs in a panel, and snapping them apart afterwards.
